減溫減壓裝置選型及計(jì)算 上海申弘閥門有限公司 之前介紹 豎式安裝自力式壓力減壓閥注意事項(xiàng),現(xiàn)在介紹減溫減壓裝置選型及計(jì)算減溫減壓器是一種將一次(新)蒸汽壓力P1、溫度t1進(jìn)行減溫減壓,使其二次蒸汽壓力P2、溫度t2達(dá)到生產(chǎn)工藝所需的要求。廣泛用于熱電廠、集中供熱、食品工業(yè)、石化工業(yè)、紡織工業(yè)、橡膠工業(yè)、造紙和紙槳工業(yè)、煙草工業(yè)、制藥等其它很多行業(yè)。在以供熱為主的電廠中主要應(yīng)用于鍋爐過熱器出口、汽輪機(jī)旁路、電廠內(nèi)部各品質(zhì)蒸汽管網(wǎng)之間的旁路系統(tǒng)等。以鍋爐過熱器出口為例,鍋爐產(chǎn)生蒸汽經(jīng)過熱器出口到汽輪機(jī)做功,汽輪機(jī)對(duì)于進(jìn)入的蒸汽參數(shù)有個(gè)范圍要求,如果過熱器出口的蒸汽參數(shù)超出汽輪機(jī)所要求的高限,就會(huì)對(duì)汽輪機(jī)造成損壞,所以必須用減溫減壓器將參數(shù)調(diào)整至適用范圍以內(nèi)。該文結(jié)合工程實(shí)踐,著重闡述減溫減壓器系統(tǒng)的設(shè)置及工藝計(jì)算。 減溫減壓裝置選型及計(jì)算通過對(duì)其CGCC 的再分析進(jìn)一步提高熱回收量,兩步工作反復(fù)進(jìn)行直到得到令人滿意的結(jié)果。Briones 等[3]成功地應(yīng)用了Liebmann 的方法進(jìn)行了降低原油精餾系統(tǒng)能耗的改造。Bagajewicz 等對(duì)Liebmann 的方法作了進(jìn)一步改進(jìn)[4]。Mamdouh等提出了一種可以同時(shí)對(duì)現(xiàn)有蒸餾系統(tǒng)及其換熱網(wǎng)絡(luò)進(jìn)行優(yōu)化改造的系統(tǒng)方法[5]。由此可見,常減壓裝置生產(chǎn)的總拔出率和節(jié)能必須同時(shí)考慮,才能實(shí)現(xiàn)裝置整體優(yōu)化。 1 流程概述 原油經(jīng)過脫前換熱網(wǎng)絡(luò)、脫鹽罐和脫后換熱網(wǎng)絡(luò)后加熱到270℃進(jìn)入初餾塔。初餾塔側(cè)線油 進(jìn)入常壓塔第28 塊板。初底油經(jīng)拔頭原油換熱系統(tǒng)換熱至300℃左右進(jìn)入常壓爐,被加熱到362℃后進(jìn)入常壓塔。常壓塔有三個(gè)側(cè)線產(chǎn)品,自上而下依次抽出常一線,常二線和常三線,首入各自汽提塔,經(jīng)蒸汽汽提后,分別用泵抽出經(jīng)換熱冷卻送出裝置。塔中部設(shè)常一中和常二中兩個(gè)中段回流,以保證塔的內(nèi)回流和熱平衡。減壓塔開設(shè)四個(gè)側(cè)線,減一線餾分用泵抽出經(jīng)換熱冷卻后部分出裝置,部分再冷卻作減頂回流。減二線餾分用泵抽出后經(jīng)換熱冷卻后部分出裝置,部分再經(jīng)換熱作減一中回流。減三線餾分用泵抽出后部分作重洗油,其余換熱冷卻后部分送出裝置,部分作減二中回流。減四線、減渣餾分用泵抽出分別換熱冷卻后送出裝置。  2 求解策略 2.1 常減壓裝置模擬與優(yōu)化 用流程模擬軟件對(duì)常減壓裝置建立模型,選擇合適的物性方法,對(duì)不同工況下進(jìn)行模擬和分析,并與裝置現(xiàn)狀進(jìn)行對(duì)比,確認(rèn)模型的可靠性。在保證產(chǎn)品質(zhì)量的基礎(chǔ)上,分析各種因素對(duì)總撥出率的影響,得到*操作參數(shù)及下一步工作中所需的冷、熱物流基礎(chǔ)數(shù)據(jù)。 2.2 進(jìn)行換熱網(wǎng)絡(luò)的*化合成 利用得到的物流數(shù)據(jù),進(jìn)行常減壓換熱網(wǎng)絡(luò)的*化合成,以確定理論上換熱網(wǎng)絡(luò)的大回收量和原油的換后溫度,為后續(xù)的優(yōu)化設(shè)計(jì)確立目標(biāo)。 2.3 對(duì)現(xiàn)有換熱網(wǎng)絡(luò)進(jìn)行*分析 為使改造工程量小,對(duì)現(xiàn)有換熱網(wǎng)絡(luò)進(jìn)行*分析,這是提高已有換熱網(wǎng)絡(luò)熱回收量的簡(jiǎn)單而比較有效的方法。經(jīng)分析,各個(gè)換熱單元熱負(fù)荷及物流進(jìn)出口溫度分配可接近*,換熱面積可作相應(yīng)的合理調(diào)整,換熱網(wǎng)絡(luò)結(jié)構(gòu)得以優(yōu)化,熱回收量大大提高。 2.4 對(duì)換熱網(wǎng)絡(luò)的進(jìn)行優(yōu)化設(shè)計(jì) 在前期所作過程模擬、換熱網(wǎng)絡(luò)的*合成和*分析等工作的基礎(chǔ)上開展進(jìn)一步的工作,對(duì)其換熱網(wǎng)絡(luò)進(jìn)行詳細(xì)的優(yōu)化設(shè)計(jì),其中包括換熱器的核算與優(yōu)化設(shè)計(jì),包括換熱網(wǎng)絡(luò)的全流程模擬等。經(jīng)過進(jìn)一步調(diào)優(yōu)后,確定出改進(jìn)后的換熱網(wǎng)絡(luò)優(yōu)化的詳細(xì)結(jié)構(gòu),該結(jié)構(gòu)將具備如下特點(diǎn):充分利用現(xiàn)有設(shè)備,新增換熱器選用大殼徑以減少冷換設(shè)備數(shù),各換熱單元熱負(fù)荷、傳熱溫差和壓強(qiáng)降分配合理。
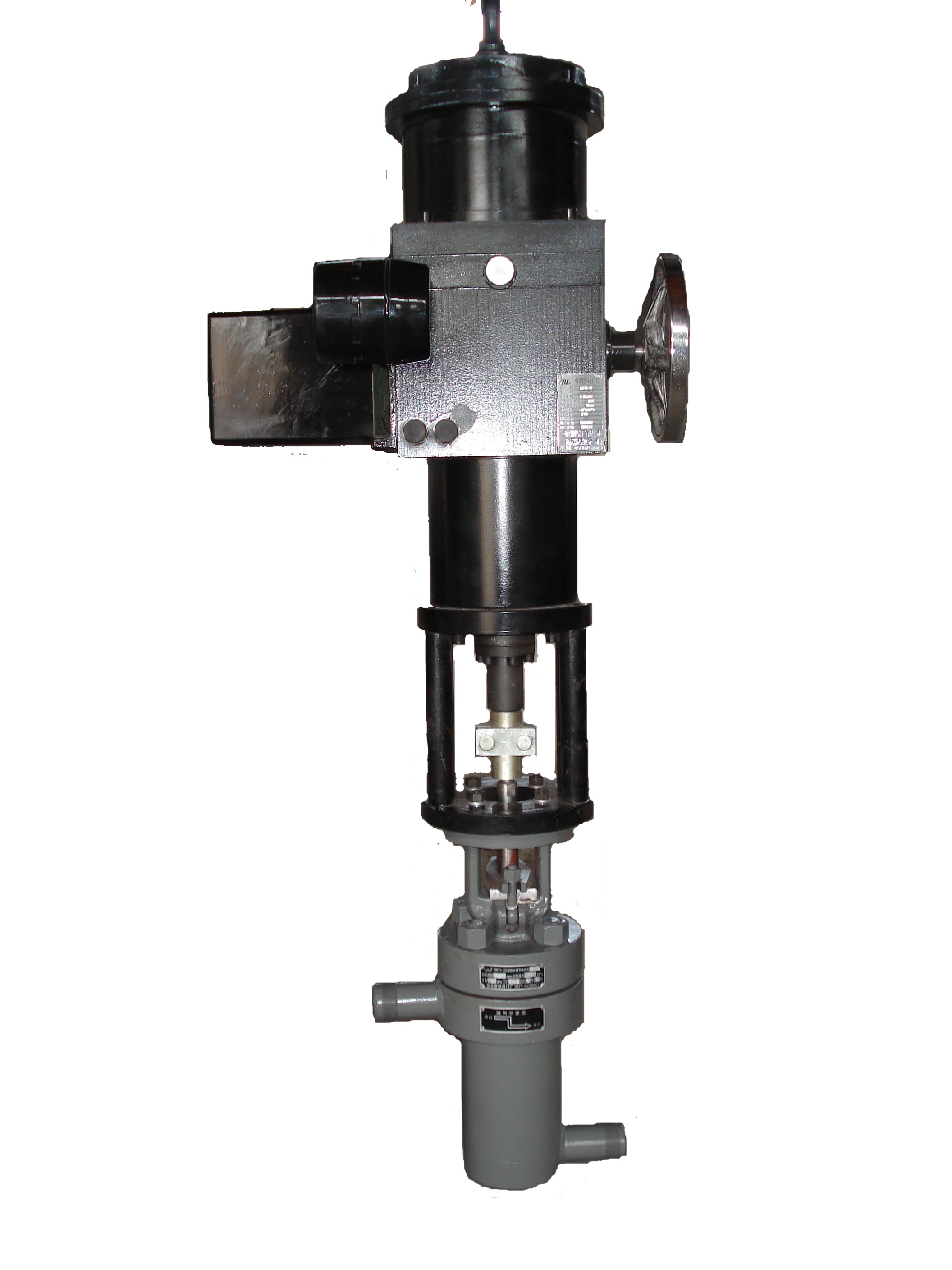 3 常減壓裝置模擬優(yōu)化 常減壓蒸餾裝置煉制原油的過程中,各線質(zhì)量流率的總和占原油加工量的百分?jǐn)?shù)稱為該原油的總拔出率。拔出率越高,所產(chǎn)生的經(jīng)濟(jì)效益也越大。由于裝置的復(fù)雜性,影響拔出率的因素有很多,如常減壓塔各線采出、塔底蒸汽量、側(cè)線蒸汽量、泵回流的流量和溫度等等。本文采用基于敏感度分析的優(yōu)化策略和方法[6],在Aspen plus軟件中建立了常減壓裝置的模型,不包括換熱網(wǎng)絡(luò),進(jìn)行模擬分析,調(diào)節(jié)這些影響參數(shù),使常減 壓的總拔出率大。
如將初頂油質(zhì)量流率作為自變量,將初頂油干點(diǎn)、常頂油干點(diǎn)、常一線干點(diǎn)、常二線閃點(diǎn)和常三線72%點(diǎn)作為因變量。橫坐標(biāo)為初頂油質(zhì)量流率,縱坐標(biāo)為各線產(chǎn)品質(zhì)量,間隔為0.5℃。由于各線產(chǎn)品質(zhì)量對(duì)應(yīng)的溫度數(shù)量級(jí)不同,所以未能在圖中列出具體數(shù)值。圖中各線產(chǎn)品對(duì)應(yīng)曲線斜率的大小與其對(duì)于初頂油質(zhì)量流率的敏感度成正比,斜率越大,敏感度越大。從圖2 可以看出,初頂油質(zhì)量流率對(duì)其干點(diǎn)影響顯著,隨著采出量的增加,干點(diǎn)急劇增大,質(zhì)量迅速降低。其對(duì)常一線干點(diǎn)(EP)、常三線72%點(diǎn)(此處將產(chǎn)品體積餾出量為72%的沸點(diǎn)數(shù)據(jù)簡(jiǎn)稱為72%點(diǎn))、常二線閃點(diǎn)影響逐個(gè)減小,對(duì)常頂油干點(diǎn)幾乎沒有影響。通過上述方法,可以得到各線產(chǎn)品質(zhì)量對(duì)其中某線采出量等影響因素的敏感度規(guī)律,為調(diào)優(yōu)提供指導(dǎo)。 對(duì)常減壓裝置進(jìn)行調(diào)優(yōu),首先根據(jù)常減壓蒸餾裝置煉制某種原油的過程模擬,從前到后、從輕到重,在不考慮產(chǎn)品質(zhì)量要求的情況下,逐個(gè)增大各線的質(zhì)量流率,即將輕餾分盡量從輕產(chǎn)品中采出,而不是置于比其重的產(chǎn)品中采出,直至達(dá)到各線的大采出量。此時(shí),各線質(zhì)量流率的總和占原油加工量的百分?jǐn)?shù)稱為該原油的理論拔出率,它是現(xiàn)有裝置煉制該種原油時(shí)的極限拔出率。根據(jù)各線產(chǎn)品質(zhì)量流率對(duì)相鄰線產(chǎn)品質(zhì)量的影響情況,如ASTM 干點(diǎn)、72%點(diǎn)和閃點(diǎn)等。根據(jù)敏感度分析結(jié)論,按照從前到后、從輕到重的原則和影響程度的大小依次減少各線的質(zhì)量流率,直到各線產(chǎn)品均能滿足質(zhì)量要求。此時(shí),各線質(zhì)量流率的總和占原油加工量的百分?jǐn)?shù)稱為該原油的實(shí)際大拔出率。實(shí)際大拔出率對(duì)應(yīng)的原油生產(chǎn)的工藝條件稱為優(yōu)化方案。 根據(jù)敏感度分析的優(yōu)化結(jié)果,和現(xiàn)有操作相比如表1 所示,裝置的實(shí)際大拔出率為68.3%,比現(xiàn)有拔出率提高3.8%,主要是提高了常頂油、常三線和減一線的采出量,降低了減二線和減三線的采出量。 
2 減溫裝置 減溫裝置通常的形式主要有一體式減溫閥,分體式減溫閥兩種;一體式的減溫閥所具有的優(yōu)點(diǎn)在于檢修與安裝都十分方便,但由于此種減溫閥的噴嘴與套筒部分筒體都處于被減溫的高溫蒸汽之中,而被減溫蒸汽的溫度又遠(yuǎn)高于減溫水的飽和溫度,通過套筒筒體的傳熱,部分減溫水已經(jīng)在筒體內(nèi)部汽化,由于一般減溫水都有著很高的壓力,產(chǎn)生的氣泡被壓縮到很小,但隨著減溫水經(jīng)噴嘴噴注到蒸汽管道中后,蒸汽的壓力小于減溫水的壓力,小氣泡在極短的時(shí)間內(nèi)在噴嘴出口處擴(kuò)容,釋放的能量較大,運(yùn)行的結(jié)果是減溫閥的噴嘴部分磨損很嚴(yán)重,影響減溫水的霧化效果。分體式減溫閥是由減溫水調(diào)節(jié)閥外加一個(gè)插入被減溫管道的噴嘴共同組成。(見圖1) 本項(xiàng)目采用的減溫裝置是由一個(gè)單獨(dú)設(shè)置在減溫減壓器外部的減溫水調(diào)節(jié)閥與設(shè)置在減溫減壓器本體尾部的環(huán)狀減溫水噴嘴組成,一次蒸汽水平進(jìn),二次蒸汽下出。(見圖2) 其優(yōu)點(diǎn)是有效的控制了減溫水在噴嘴內(nèi)部的汽化,多噴嘴在減溫段噴射,保證減溫水與一次蒸汽的充分混合,再結(jié)合角式減壓裝置,即使在蒸汽流速較低的情況下,減溫水在與一次蒸汽混合后向下流動(dòng),也可有效的控制低溫的減溫水汽化之前由于重力的因素與高溫的管道內(nèi)壁接觸而產(chǎn)生管道材料的淬脆現(xiàn)象。 上面兩圖中,水平設(shè)置的減溫管道在蒸汽流速較低或者噴嘴霧化效果不佳的情況下極易產(chǎn)生金屬淬脆現(xiàn)象,將影響管道的安全運(yùn)行。豎直設(shè)置的減溫管道減溫水小液滴隨二次蒸汽向下流動(dòng),可有效的避免未汽化的液滴與高溫金屬內(nèi)壁的接觸,從而減小發(fā)生金屬淬脆現(xiàn)象的產(chǎn)生。 接下來根據(jù)下式: G2=G3(H1- H3)/( H1- H2) G2―減溫水流量;H2―減溫水焓;H1 ―一次蒸汽焓;H3―二次蒸汽焓;G3―二次蒸汽流量。 根據(jù)250t/h的4.6MPa(G)、405℃二次蒸汽量,計(jì)算得到減溫水量為:20.2t/h;而后供貨商根據(jù)本設(shè)備所選噴嘴特性及霧化程度提供霧化后的減溫水所需汽化時(shí)間,根據(jù)二次蒸汽流速計(jì)算得到減溫混合段長(zhǎng)度,對(duì)減溫減壓器后二次蒸汽管道進(jìn)行設(shè)置。  3 安全排放裝置的選型和計(jì)算步驟主要有下面幾點(diǎn) (1)減溫減壓器的安全閥其排放介質(zhì)為過熱蒸汽,我們一般應(yīng)選取全啟式安全閥。 (2)根據(jù)被保護(hù)管道的設(shè)計(jì)壓力確定安全閥的整定壓力。 高壓蒸汽管道設(shè)計(jì)壓力:5.2MPa(a) 安全閥整定壓力:Ps=5.2MPa(a) 積聚壓力Pa=0.03Ps=0.156 MPa(a) 高泄放壓力:Pm=Ps+Pa=5.2+ 0.156=5.356 MPa(a) (3)確定安全閥泄放量。 上海申弘閥門有限公司主營(yíng)閥門有:減壓閥(氣體減壓閥,可調(diào)式減壓閥,波紋管減壓閥,活塞式減壓閥因?yàn)闇p溫減壓器本身是由壓力調(diào)節(jié)閥與溫度調(diào)節(jié)閥組成,故其安全泄放量應(yīng)定性的確定為控制閥故障及減溫減壓器后系統(tǒng)閥門誤關(guān)閉兩種情況。 ①減溫減壓器后系統(tǒng)閥門誤關(guān)閉工況時(shí),其安全閥泄放量應(yīng)為被關(guān)閉管道的正常大流量; ②控制閥故障工況時(shí),其安全閥泄放量應(yīng)根據(jù)下式確定。 W―安全閥泄放質(zhì)量流量,kg/h;Cv1―控制閥的Cv值;Cv2―控制閥小流量下的Cv值;Ph―高壓側(cè)工作壓力,MPa;Gg ―汽相密度,kg/m3;T―泄放溫度,K。 但在熱電廠內(nèi)的減溫減壓器作為汽輪機(jī)旁路時(shí),其控制方式與一般過程控制調(diào)節(jié)方式的不同之處在于其大多數(shù)情況不是持續(xù)的過程控制,而是作為事故工況下,比如抽凝式汽輪機(jī)跳車時(shí),作為補(bǔ)充工業(yè)可調(diào)抽汽因抽凝機(jī)組跳車所損失的抽汽量的手段,故我認(rèn)為一般此類型減溫減壓器計(jì)算安全泄放量時(shí)可考慮將減溫減壓器二次蒸汽的大流量作為其安全泄放量。 根據(jù)以上兩種工況,我們選定安全閥的泄放量為250t/h(二次蒸汽全量放空),但由于一般與界外整個(gè)化工裝置區(qū)域的管網(wǎng)相比,動(dòng)力中心內(nèi)部管網(wǎng)總的容積并不大,這里考慮并聯(lián)兩臺(tái)125t/h排量的安全閥,且設(shè)置不同的整定壓力,使其在管道超壓時(shí)可依次起跳,以盡可能減小安全閥起跳對(duì)管網(wǎng)壓力的影響。 (4)根據(jù)泄放量計(jì)算安全閥的小泄放面積。 根據(jù)美國石油學(xué)會(huì)標(biāo)準(zhǔn)API RP-520中的規(guī)定首先應(yīng)判斷是否為臨界流動(dòng) Pb ―安全閥背壓,MPa;Pcf― 臨界流動(dòng)壓力,MPa;P― 泄放壓力,MPa;k―絕熱指數(shù)。 因安全閥后為接消音器排大氣,故根據(jù)安全閥泄放壓力計(jì)算屬臨界流動(dòng)。氣體或蒸汽在臨界流動(dòng)條件下的小泄放面積: a= a―小泄放面積,mm2;W―質(zhì)量泄放流量,kg/h;C0―流量系數(shù),對(duì)于全啟式安全閥取C0=0.67;X―氣體特性系數(shù),取349.4;P―泄放壓力,MPa;Kb―背壓修正系數(shù),彈簧式安全閥取Kb=1.0;T―泄放溫度,K;Z―氣體壓縮因子;M―分子量,水蒸汽為18。 根據(jù)125t/h的泄放量,計(jì)算可得小泄放面積為:a=7682.01mm2,故,安全閥喉徑為:d=98.90mm,根據(jù)計(jì)算出的喉徑,初步選取國標(biāo)安全閥,型號(hào)為:DN150 A48Y-64I,完成安全閥采購數(shù)據(jù)表。至此,關(guān)于減溫減壓器系統(tǒng)各裝置的設(shè)置及選型計(jì)算完成。 綜上所述,我們?cè)阪?zhèn)海煉化100萬噸/年乙烯工程動(dòng)力中心內(nèi)所選擇的減溫減壓器為水平進(jìn)下出的一體式減溫減壓器,減溫水調(diào)節(jié)閥至于減溫減壓器外部,一次蒸汽:操作壓力12.3MPa(G),操作溫度535℃,流量:229.8t/h;二次蒸汽操作壓力4.6MPa(G),操作溫度405℃,流量:250t/h;減溫水:操作壓6.0MPa(G),操作溫度158℃,流量:20.2t/h;減溫減壓器安全排放裝置選擇兩臺(tái)125t/h的安全閥,整定壓力分別為:Ps=5.2MPa(a)和Ps=5.1MPa(a),初部選取型號(hào)為:DN150 A48Y-64I。與本產(chǎn)品相關(guān)論文:Y42X-600LB美標(biāo)彈簧薄膜式減壓閥
|