減壓閥的結構形式設計 減壓閥的結構形式 減壓閥結構 減壓閥設計 減壓閥構造 減壓閥設計 之前介紹減壓閥前后的壓力變化,現(xiàn)在介紹減壓閥的結構形式設計介紹了一種減壓閥的總體結構形式,并對其在使用過程中發(fā)現(xiàn)的問題進行改進優(yōu)化,提高了其使用可靠性。通過對比分析發(fā)現(xiàn),減壓閥的密封形式與導向軸的導向方式對減壓閥的性能影響較大。 減壓閥按結構形式可分為薄膜式、彈簧薄膜式、活塞式、杠桿式和波紋管式;按閥座數(shù)目可人為單座式和雙座式;按閥瓣的位置不同可分為正作用式和反作用式。先導式減壓閥當減壓閥的輸出壓力較高或通徑較大時,用調壓彈簧直接調壓,則彈簧剛度必然過大,流量變化時,輸出壓力波動較大,閥的結構尺寸也將增大。為了克服這些缺點,可采用先導式減壓閥。先導式減壓閥的工作原理與直動式的基本相同。先導式減壓閥所用的調壓氣體,是由小型的直動式減壓閥供給的。若把小型直動式減壓閥裝在閥體內部,則稱為內部先導式減壓閥;若將小型直動式減壓閥裝在主閥體外部,則稱為外部先導式減壓閥。 減壓閥的構造類型很多,以往常見的有薄膜式、內彈簧活塞式等。減壓閥的基本作用原理是*閥內流道對水流的局部阻力降低水壓,水壓降的范圍由連接閥瓣的薄膜或活塞兩側的進出口水壓差自動調節(jié)。近年來又出現(xiàn)一些新型減壓閥,如定比式減壓閥,其構造原理如圖14.2-2所示。定比減壓原理是利用閥體中浮動活塞的水壓比控制,進出口端減壓比與進出口側活塞面積比成反比。這種減壓閥工作平穩(wěn)無振動;閥體內無彈簧,故無彈簧銹蝕、金屬疲勞失效之慮;密封性能良好不滲漏,因而既減動壓(水流動時)又減靜壓(流量為0時);特別是在減壓的同時不影響水流量。減壓閥通常有DN50~DN100等多種規(guī)格,閥前、后的工作壓力分別為<1MPa和0.1~0.5MPa,調壓范圍誤差為 5%~10%。 應該看到,水流通過減壓閥雖有很大的水頭損失,但由于減少了水的浪費并使系統(tǒng)流量分布合理、改善了系統(tǒng)布局與工況,因此總體上講仍是節(jié)能的。 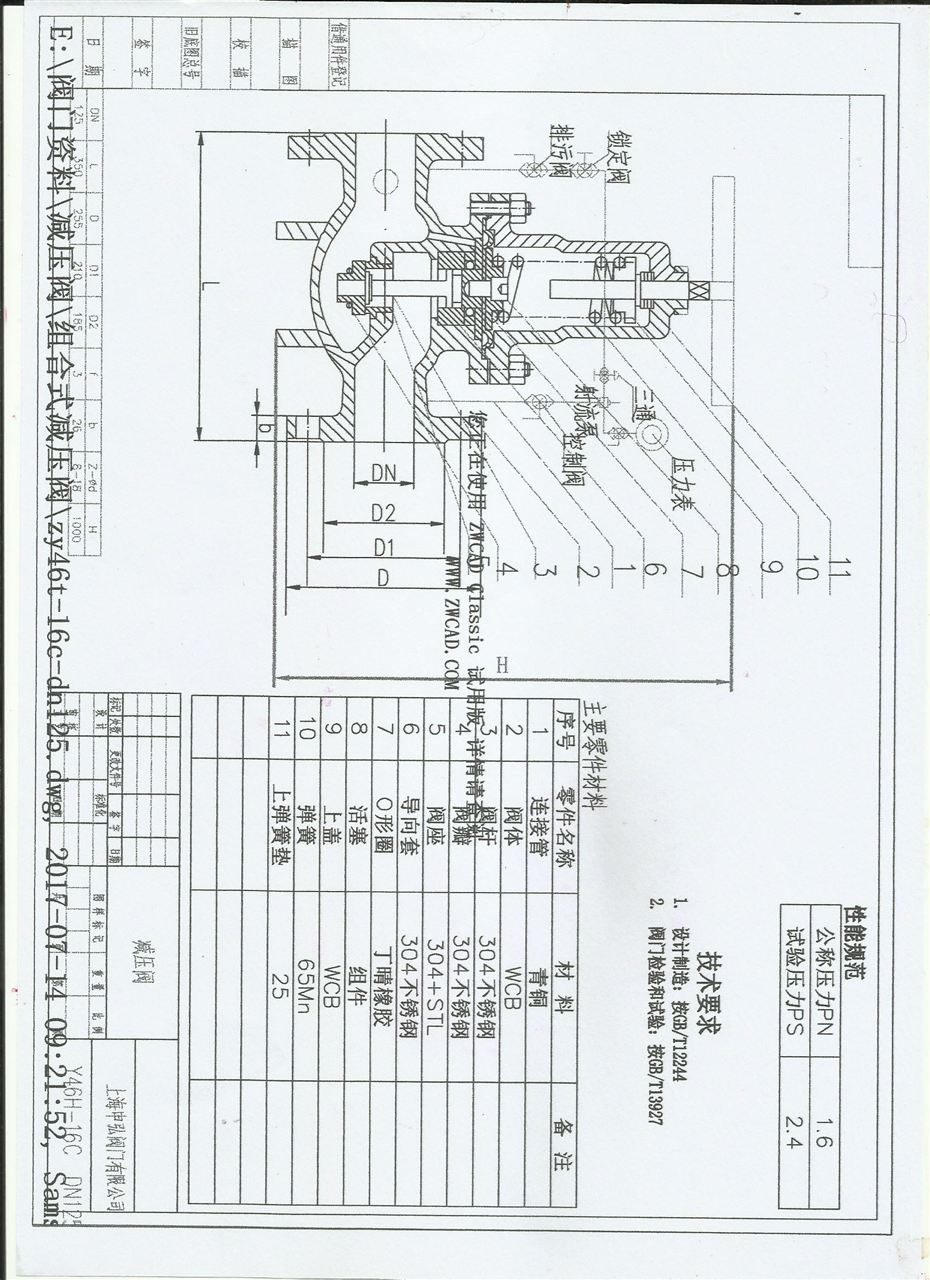
【關鍵詞】減壓閥;密封;導向 1.減壓閥的結構形式設計引言 減壓閥是一種目前被廣泛采用的安全泄壓裝置。而彈簧式減壓閥是其中比較典型的一種。它是采用彈簧的壓力作用為加壓載荷,并通過調節(jié)彈簧壓力的大小來調整減壓閥的開啟壓力。當系統(tǒng)中壓力超過允許值后,它能夠自動開啟并把過剩的系統(tǒng)介質排到大氣或低壓系統(tǒng)中,從而達到泄壓的目的。當壓力降到某一數(shù)值時,它又能自動迅速關閉,維持系統(tǒng)的正常運行。 如圖1所示,某產品浮囊在充氣展開以及回收上浮過程中,環(huán)境壓力逐漸減小,浮囊內的壓力會增大,由減壓閥將浮囊內多余的氣體排掉,保持浮囊內外壓差恒定,從而保持浮囊的安全。減壓閥關閉時能要能可靠的密封,開啟時要有靈敏的排氣功能,將多余的氣體排出。 可調式減壓閥的結構特點: 1、啟閉無摩擦:完*了閥門因密封面之間相互摩擦而影響密封的問題; 2、上裝式結構:對裝在管道上的閥門可直接在線檢查與維修,能有效減少裝置停車,降低成本; 3、單閥座設計:消除了閥門中腔介質因異常升壓而影響使用安全的問題; 4、低扭矩設計:特殊結構設計的閥桿,只需配一個小手輪閥門就能輕松啟閉; 5、楔形密封結構:閥門是靠閥桿提供的機械力,將球楔壓到閥座上而密封,使閥門的密封性不受管線壓差變化的影響,在各種工況下密封性能都有可靠保證; 6、可調式減壓閥的密封面的自清潔結構:當球體傾離閥座時,管線中的流體沿球體密封面成360°均勻通過,不僅消除了高速流體對閥座局部的沖刷,也沖走了密封面上的聚積物,達到自清潔的目的。 
2.總體結構 如圖2所示,減壓閥采用簡單的機械壓差式控制閥結構,壓力控制通道與流量控制通道合二為一,通過彈簧的壓縮控制浮囊內外的壓差,當壓差小與設定壓力時,減壓閥閥芯關閉,保證浮囊密封;當壓差大于設定壓力時;減壓閥閥芯打開,排掉氣體,平衡壓力。 減壓閥的壓力設定值主要受到兩方面因素的影響:浮囊的強度和充氣后浮囊的展開狀態(tài)。設定壓差大則浮囊展開后“硬度”大,能較好保持浮囊圓柱狀的外形,從而保持設計要求的浮力,但對浮囊的強度要求也越高;設定壓差小,浮囊的強度要求低,但浮囊膨脹后偏“軟”,上浮到水面后若溫度降低,沒有相應的壓力儲備,浮力會減小。  3.計算分析 上海申弘閥門有限公司主營閥門有:減壓閥(組合式減壓閥,可調式減壓閥,自力式減壓閥安裝在浮囊上的減壓閥即要有好的密封性能還要有靈敏的排氣功能,這樣減壓閥中彈簧力的選擇一定要合理,參照某產品減壓閥的結構形式及使用情況,結合本產品的實際及上浮過程中的排氣通徑,估算出保證減壓閥密封性能的彈簧預緊壓力。根據(jù)減壓閥的指標要求,在進行彈簧設計時,要求彈簧預緊力可調。 當閥門從進口端給水時,水流過針閥進入主閥控制室,出口壓力通過導管作用到導閥上。當出口壓力高于導閥彈簧設定值時,導閥關閉。控制室停止排水,此時主閥控制室內壓力升高并關閉主閥,出口壓力不再升高。當閥門出口壓力降到導閥彈簧設定壓力時,導閥開啟,控制室向下游排水。由于導閥系統(tǒng)排水量大于針閥的進水量,主閥控制室壓力下降。進口壓力使主閥開啟。在穩(wěn)定狀態(tài)下,控制室進水、排水相同,主閥開度不變,出口壓力穩(wěn)定。調節(jié)導閥彈簧即可設定出口壓力。 先導式減壓閥200X如何調試壓差: 減壓閥的前端壓力必須大于導閥的設定壓力,后端壓力必須小于導閥的設定壓力,這樣減壓閥才能工作。有壓差的前提條件是閥前壓力大于導閥的設定壓力,當閥前壓力低于等于減壓閥設計的大閥后壓力時,是無法調出明顯壓差的。閥后壓力調整是通過導閥調整螺桿進行的,松緊螺帽就能進行調整,一般情況下(視導閥結構)螺桿旋入輸出壓力減小。
 3.1 減壓排氣計算 試驗彈在上浮的過程中,回收浮囊的背壓不斷減小,需要開啟減壓閥泄掉多余的氣體,以平衡內外壓差,保持浮囊穩(wěn)定工作,減壓閥打開時的氣體流量: 式中,:有效截面積;:上游壓力;:壓差;:上游熱力學溫度。 減壓閥開口截面積:,有效截面積,查表可知:,則當上浮到水面位置,浮囊內的壓力值小,此時流量小。 假設回收浮囊內氣體的初始狀態(tài)為:;上浮后減壓閥會排出部分氣體,此時浮囊內氣體的狀態(tài)為:;排出的氣體狀態(tài)為:,則有: 顯然,在上浮過程中由于水介質的作用,回收浮囊內的氣體會降溫,會減小,在此為簡化計算,假溫度不下降,,此時排出的氣體大,所以: 試驗彈勻速上浮時,速度達到大值,環(huán)境壓力也變化快,此時的大,當上浮到水面時環(huán)境背壓小,即小,則此時需要排出的氣體大。 有以上分析可知:在設計必須保證減壓閥的流量大于回收浮囊需要排出的氣體量,即:時,才能可靠保證浮囊安全工作。 3.2 彈簧計算 彈簧作為減壓閥的壓力調節(jié)重要零件,用來平衡減壓閥內外壓差并使其密封。在該減壓閥彈簧力計算中,進行以下簡化: 1)閥芯與閥體的接觸面之間涂敷潤滑脂,不考慮其摩擦力影響; 2)閥芯質量較小,不考慮閥芯的重量影響。 根據(jù)上述簡化計算條件并結合減壓閥的各項指標要求并根據(jù)其排氣通徑尺寸,進行彈簧的設計計算,詳細設計可參考《機械設計手冊(四)》,并結合《普通圓柱螺旋壓縮彈簧尺寸及參數(shù)》(GB/T 2089-2009)對設計進行調整,使之符合相關規(guī)范。
 4.影響減壓閥密封的因素 由于減壓閥控制的壓差較小、精度高。對此,需對減壓閥進行調試測試,使其符合要求,若超差,可進行機械調整。在減壓閥調試過程中,發(fā)現(xiàn)減壓閥開啟后閉合比較困難與閉合壓力達不到指標要求的現(xiàn)象,調試成功率較低。 針對上述減壓閥調試過程中出現(xiàn)的問題并結合減壓閥實際工作過程,分析可能影響減壓閥密封性能與閉合壓力的各種因素: 1)減壓閥長時間不工作時,彈簧的全部力作用在閥芯的密封面上,若密封面寬度過窄,在較大的壓力作用下,可能造成密封面損傷,引起密封不良。同時,若閥芯的密封材料采用較軟的橡膠材料,容易導致較深的壓痕,產生塑性變形,降低了其密封性能。 2)密封面表面質量的好壞,直接影響關閉件密封性。密封面的幾何精度和表面光潔度與密封性有很大的關系。若加工方法不當,金屬密封面在加工中出現(xiàn)的微觀不平以及波紋都會影響密封效果。 3)在同等壓力、溫度情況下,粘性大的介質比粘性小的介質泄漏量要小。液體介質比氣體介質易密封。因此要考慮到閥設計時的許用介質。介質溫度會引起密封面熱變形,在密封材料中會造成熱梯度,引起密封面翹曲。 4)減壓閥德閥芯是核心組件,其密封方式、密封材料以及導向定位的選擇都會減壓閥的密封可靠性產生影響。其中,密封方式主要有:軸向式、錐臺式與錐形式。其中,若閥芯與閥體的導向定位選擇不合理或加工精度達不到要求,均會造成閥芯的穩(wěn)定性不足,彈簧壓力不均,降低閥芯與閥體密封面之間的密封性能。 通過對減壓閥在調試過程中出現(xiàn)的各種情況進行觀察,發(fā)現(xiàn)以下主要現(xiàn)象: 1)與導向軸粘接的橡膠墊材料較軟,容易出現(xiàn)壓痕,粘接固定在導向軸的橡膠墊有較深的壓痕; 2)橡膠密封墊與導向軸粘接后表面凹凸不平,影響其密封性能; 3)與閥芯接觸的密封面加工精度較差,存在加工刀痕; 4)預緊力調節(jié)蓋與導向軸之間間隙過大導致導向軸晃動幅度較大,影響與閥芯上的彈簧軸向壓縮性能。 5.減壓閥的改進與優(yōu)化 通過上述對影響減壓閥密封與閉合性能的因素分析,以及相關現(xiàn)象的總結,并結合本產品實際使用要求與環(huán)境,對減壓閥進行如下系列優(yōu)化改進,如圖3、4所示。 1)增加導向軸與閥體間的導向定位,并增大導向軸與預緊力調節(jié)蓋的導向尺寸。通過此項改進與優(yōu)化,明顯地降低閥芯開啟閉合運動時的晃動,提高閥芯的穩(wěn)定性,從而保證減壓閥彈簧壓力的均勻性; 2)將橡膠墊軸向壓密封方式,改為錐形〇形圈密封方式,且閥芯與閥體的密封方式由軸向式改為錐臺式。通過采取此項措施,能避免橡膠墊因粘接固定產生的凹凸不平,以及橡膠材料過軟所導致的壓痕或損傷,終對減壓閥的密封與閉合性能造成的不利影響。采用錐臺式密封方式,能改善軸向密封因彈簧壓力不均所造成的不利影響,增加閥芯與閥體錐面的擠壓接觸,從而提高其密封性能與閉合穩(wěn)定性。 3)提高減壓閥密封面的加工光潔度,并將加工材料由鋁合金改為合金鋼并進行電鍍處理。通過加工工藝與材料的改進,提高密封面的密封性能。同時,因鋁合金材料在高溫氣體作用下可能產生變形,因此,通過合金鋼材料能降低高溫氣體對減壓閥結構所造成不不利影響。 在對減壓閥進行上述系列優(yōu)化改進后,在減壓閥反復開啟、閉合調試檢測過程中,減壓閥密封性能大幅度提高,開啟、閉合壓力性能指標穩(wěn)定,調試成功率達到85%以上,大幅度節(jié)省了減壓閥的加工成本,提高了其重復利用率。
 6.總結 通過本文上述分析可以發(fā)現(xiàn),導致彈簧式減壓閥密封與閉合性能不穩(wěn)定的因素很多,而且這些因素之間的關系也很復雜,要想保證減壓閥密封狀況良好,保障被保護系統(tǒng)的安全性,需要設計過程中認真細致的考慮各方面的影響,要保證其較好的可靠性,在設計中必須考慮以下幾點。 首先,閥芯密封結構形式,需要根據(jù)實際使用要求選取,如軸向式、錐臺式與錐形式;其次,閥芯的導向定位,在設計中需合理選擇定位位置與形式,盡可能提高密封閥芯的穩(wěn)定性;后,減壓閥加工材料、配合面加工精度與光潔度,根據(jù)其使用環(huán)境進行加工材料選取,配合面加工精度與光潔度必須嚴格控制。與本產品相關論文:波紋管減壓閥波紋管材料
|